工业控制系统的基本概念与组成
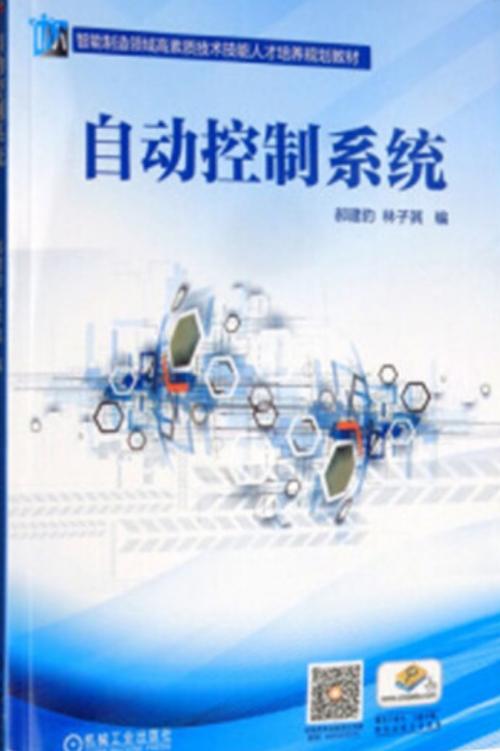
工业控制系统是指用于监测和控制工业过程的硬件和软件系统,它通过传感器、执行器、控制器等设备实现对生产过程的自动化控制。典型的工业控制系统由以下几个核心组件构成:可编程逻辑控制器(PLC
)、分布式控制系统(DCS
)、监控与数据采集系统(SCADA
)、人机界面(HMI)以及各种现场总线网络。这些组件协同工作,形成一个完整的控制闭环,确保工业生产过程的安全、稳定和高效运行。
工业控制系统的关键技术
1. 可编程逻辑控制器(PLC)技术
PLC是工业控制系统的核心设备,它采用可编程存储器来存储指令,执行逻辑运算、顺序控制、定时、计数和算术运算等操作。现代PLC具有模块化设计、高可靠性、抗干扰能力强等特点,能够适应各种恶劣的工业环境。随着技术的发展,PLC的处理能力不断增强,支持的功能也日益丰富,包括运动控制、过程控制、网络通信等高级功能。
2. 分布式控制系统(DCS)架构
DCS是一种分散控制、集中管理的控制系统架构,特别适用于大型连续过程工业,如石油化工、电力等行业。DCS通过将控制功能分散到多个控制器中,同时保持操作管理的集中化,实现了控制系统的高可靠性和灵活性。现代DCS系统还集成了先进的过程优化算法、故障诊断功能和预测性维护能力,大大提升了工业生产的智能化水平。
工业控制系统的典型应用场景
工业控制系统广泛应用于各个工业领域,包括但不限于:制造业生产线控制、电力系统监控与调度、石油化工过程控制、水处理与供水系统、交通运输控制系统等。在智能制造领域,工业控制系统与物联网、大数据、人工智能等技术深度融合,实现了生产过程的数字化、网络化和智能化,推动着传统制造业向智能制造转型升级。
工业控制系统的安全挑战与防护措施
随着工业控制系统与IT网络的深度融合,网络安全问题日益突出。工业控制系统面临着病毒攻击、网络入侵、数据泄露等多种安全威胁。为确保工业控制系统的安全运行,需要采取多层次的安全防护措施,包括网络隔离、访问控制、数据加密、安全审计等。同时,还需要建立完善的安全管理制度,提高人员安全意识,形成技术与管理相结合的综合防护体系。
工业控制系统的未来发展趋势
未来工业控制系统将朝着以下几个方向发展:是智能化,通过引入人工智能技术,实现控制系统的自学习、自适应和自主决策能力;是数字化,利用数字孪生技术构建虚拟控制系统,实现虚实结合的控制优化;再次是网络化,基于5G、工业互联网等技术,构建更加开放、灵活的工业控制网络;是绿色化,通过优化控制算法和节能技术,降低工业生产的能耗和排放,推动工业可持续发展。
工业控制系统作为工业自动化和智能制造的核心技术,正在经历深刻的变革与创新。随着新技术的不断涌现和应用场景的持续拓展,工业控制系统将在推动工业转型升级、提升制造业竞争力方面发挥更加重要的作用。企业需要紧跟技术发展趋势,加强工业控制系统的建设和优化,才能在激烈的市场竞争中保持领先优势。
常见问题解答
- 工业控制系统与IT系统有什么区别?
工业控制系统更强调实时性、可靠性和安全性,通常采用专用硬件和操作系统,而IT系统则更注重数据处理和通用性。ICS对系统中断的容忍度极低,且运行环境往往更加恶劣。
- 如何选择适合的工业控制系统?
选择工业控制系统需要考虑多个因素,包括控制规模、工艺复杂度、实时性要求、可靠性需求、预算限制等。小型离散制造通常选用PLC系统,大型连续过程工业则更适合DCS系统。
- 工业4.0对工业控制系统有哪些影响?
工业4.0推动了工业控制系统的智能化、网络化和数字化变革。要求ICS具备更强的数据采集和分析能力,支持云端协同和边缘计算,实现更加灵活和高效的生产控制。